OOKSAN IMT Co., Ltd. has accumulated technologies
through its long experience and research.
Based on them, the company does the best to supply better equipment
in order to live up to customers’ expectations.
Development of High-speed Stacker Crane Technology in High-temperature Setting
(1000class clean)
With our multi-year technology know-how and various solutions, we research the stacker crane that fits high-temperature and high-speed driving settings, and design the equipment applicable to 1000 Class Clean.
- National support project: Technology Innovation Development (joint development of technology with Pusan National University)
- Research period: Aug. 1, 2012 to Jul. 31, 2014
- Total research cost: about 900 million KRW
Structural and dynamics analysis
Specification |
Specialties |
Environment |
Cleanroom |
- Testing in the severe condition of over 65℃ for finding the equipment’s lifespan at high temperature
- Excellent stop level
- Structural design to minimize the shaking displacement of the upper side
- Electroless N1 plating, Non-refined powder coating
|
Driving speed |
300m/min |
Elevation speed |
60m/min |
Forking speed |
7sec/tack time, 0.85st |
lift Stroke |
3150mm |
Development of highly-efficient sintering device for manufacturing positive electrode active material (secondary cell)
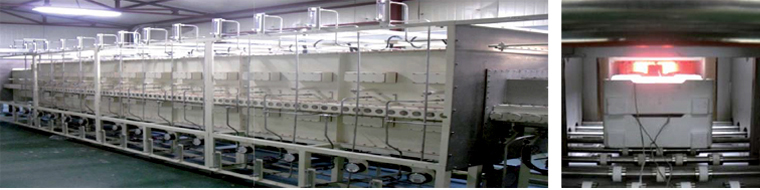
A sintering furnace for manufacturing the positive electrode active materials of lithium secondary cells is capable of removing smoothly the gases (CO2, CO) generated at the time of synthesizing positive electrode active materials and thereby of making it easy to synthesize such materials. Our company developed the highly-efficient sintering device for manufacturing the positive electrode active materials, which supports composition of multiple atmospheric gases and uniform furnace temperature.
- National support project: Energy Resource Technology Development (joint development of technology with Pusan National University)
- Research period: Jun. 1, 2010 to May 31, 2012
- Total research cost: about 1.1 billion KRW
- Design based on conditional current and temperature analysis
- Development of efficient air supply and exhaust system
- Implementation of uniform internal temperature
- Remote control and monitoring system
Upper & Side Supply Lower Exhaust System
- Smooth contact of gases (e.g., O2) for synthesis
- Material rise speed 10% up by convention heat -> Time shortening
- Efficient at CO2 exhaust
→ CO2 generated after synthesis stays on the bottom
→ Efficient removal of CO2 through lower exhaust
Precision research through thermal analysis |
Design & pilot-test through flow field analysis |
Uniform temperature |
±5˚C |
Supply & exhaust system |
Efficient supply and exhaust system |
Driving type |
SIC Roller, Friction driving |
Efficiency |
Two-layer loading based productivity improvement and energy saving effect |
Final goals |
- Localization and commercialization of the sintering furnace for manufacturing positive electrode active materials of lithium-ion cells
- Development of the highly-efficient sintering furnace with over 150% improved productivity (two layers)
|